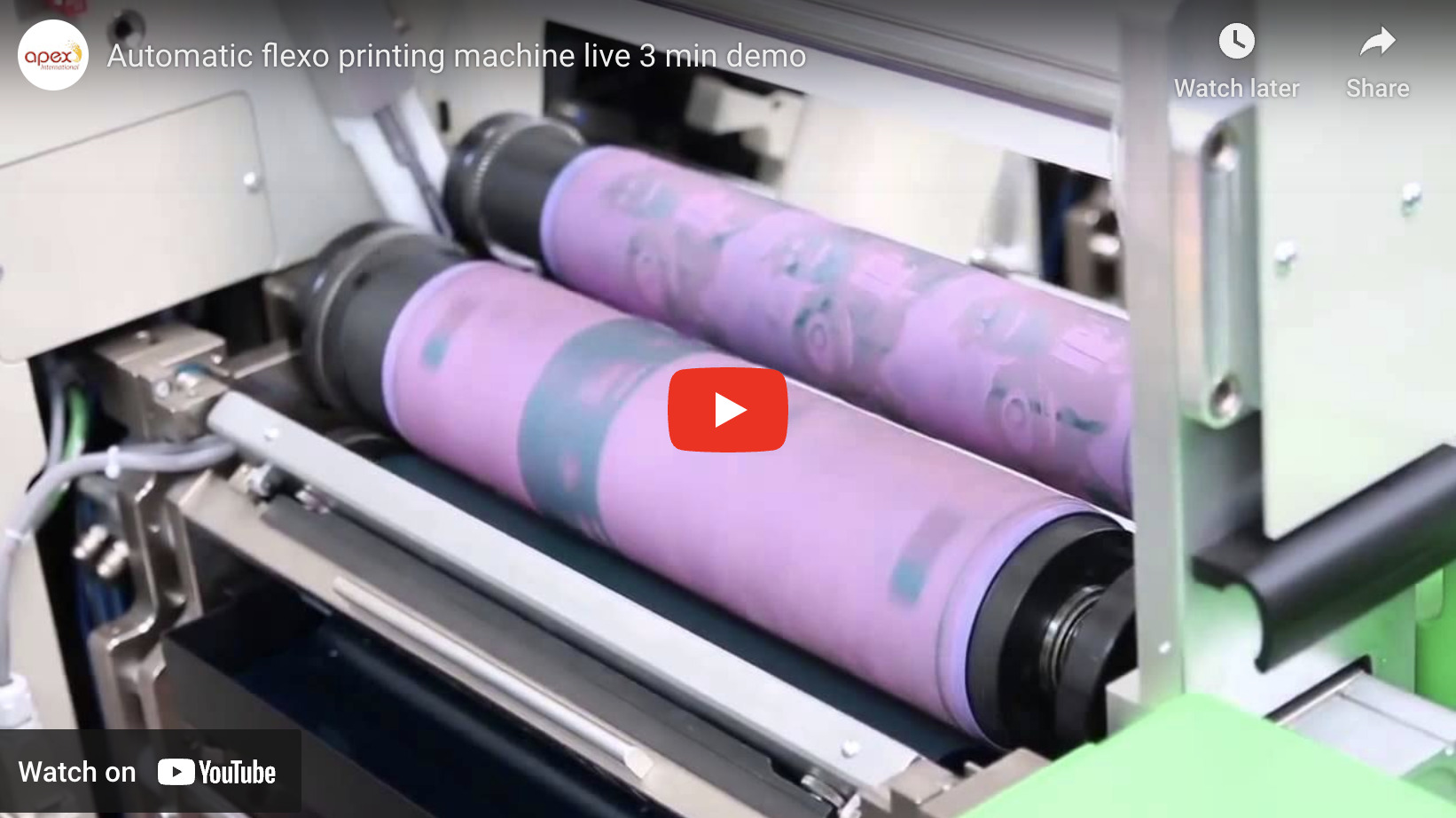
Videos
The Apex Academy is a resource center designed to provide reference, education, and answers to frequently asked questions surrounding the printing industry. Ever wonder why most global OEMS trust the Apex brand? Our dedicated team of experts have been investing their time and talents developing modern, innovative technologies in the printing industry for over 150 years. Access the knowledge of our worldwide experts using our extensive resource center.